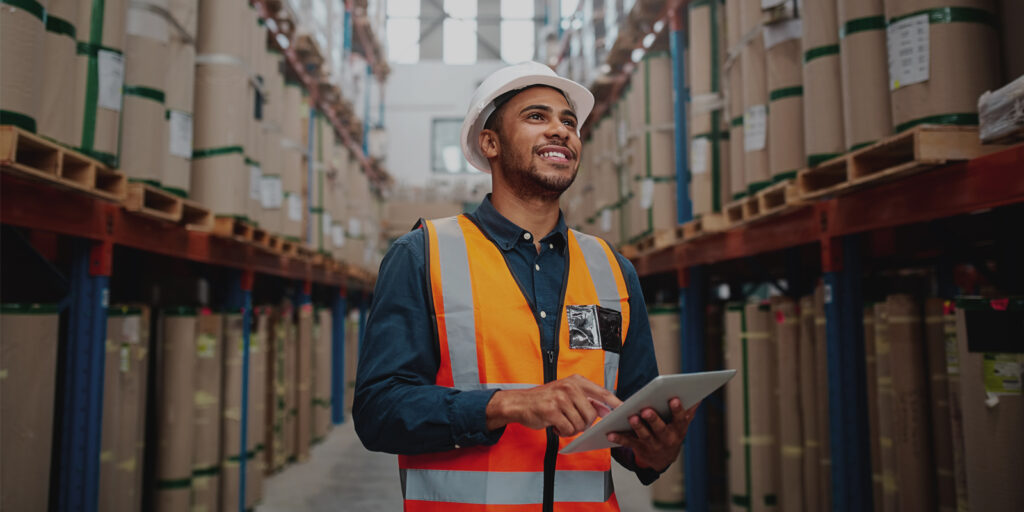
Summary:
Instead of focusing solely on ROI, manufacturing organizations need to also understand their total cost of ownership (TCO) for each asset. However, organizations need the right infrastructure to support the technology needed to improve TCO.
Many manufacturers focus on increasing their return on investment (ROI) for purchases. However, ROI is only one piece of the puzzle. Your ROI for a specific piece of equipment tells you the benefits, usually a cost saving, of using the machine. If the asset constantly needs repairs and replacement, even a purchase that initially indicates having a high ROI can hurt your bottom line.
To get a full picture of the impact of a machine on operations and the budget, manufacturers are increasingly focusing on total cost of ownership (TCO), which is the total costs incurred over the life cycle of the specific asset. When you measure TCO, you include all costs related to purchasing, owning and operating an asset, both direct and indirect.
By focusing on TCO, manufacturers can reduce their risk as well as unexpected costs. While many organizations initially track this financial estimation to reduce expenses, the metric also helps monitor sustainability of equipment and its performance.
Calculating your TCO
ROI is often simple to calculate, just by using one of the many online calculators that are available. However, TCO is more complex and challenging to determine. In addition to a wide range of factors to consider, many data points vary widely between assets. For example, the depreciation on one machine may be much faster than another machine. Because a one-size-fits-all calculators doesn’t exist, manufacturers often neglect this metric.
Calculating your TCO starts by using proper data visualization strategies to get visibility into all related data. In addition to the purchase price and maintenance, be sure to include other indirect expenses, such as warranty and downtime due to maintenance issues. By reviewing the data points for each piece of equipment separately, you’ll gain an understanding of the unique properties that affect its TCO. Next, set up a collection and tracking process for each of the factors to continually monitor total expenses.
Lowering your TCO
By using technology in various ways, manufacturers can improve efficiency, reduce operational costs and optimize resource utilization. These measures often make a significant impact on lowering the TCO of assets. When multiplied across multiple assets in a factory, the benefits provided by automation for lowering the TCO often adds up to a significant savings.
Here are some ways technology helps achieve this:
- Automation: Every time an employee completes a manual task, you increase production time, cost and the risk of human error. Materials handling presents an opportunity for automation for many manufacturers, such as loading/unloading materials into storage bays, moving products in the field and positioning heavy components in the assembly process.
By turning to automation, manufacturers can decrease these issues and, in turn, increase cost savings and improve productivity. Respondents to the survey reported reduced expenses as the biggest benefit of automation. Because these reduced expenses often relate to equipment, automating tasks makes a big impact on TCO.
- Cloud computing: Purchasing and maintaining on-premises infrastructure is expensive and time consuming. Cloud services enable businesses to access IT resources on demand, reducing the need for upfront investments in hardware and software. This also minimizes maintenance costs and allows for better resource scaling as business needs change. G2 found that over 40% of companies have fully achieved the expected benefits, including improved service levels (43%), business enablement (45%) and business continuity (42%) from cloud adoption.
- Energy efficiency: With the increased customer emphasis on sustainability, many manufacturers are prioritizing saving energy. Modern technology often comes with improved energy efficiency, which reduces power consumption and associated costs in both hardware and facility management. By purchasing energy-efficient technology, your manufacturing organization can lower costs through reducing TCO. Technology such as IoT devices to detect waste and AI-based tools to predict consumption can also help you measure energy usage.
- Remote work capabilities: Some positions in manufacturing need to be on the factory floor. But many employees, such as those in marketing, finance and supply chain, can successfully complete their tasks remotely at least some of the time. Global Workplace Analytics estimates that a typical U.S. employer can save an average of $11,000 per half-time telecommuter per year through savings on increased productivity, lower real estate costs, reduced absenteeism and turnover, and better disaster preparedness.
- Improved collaboration and communication: Successful operations, especially those involving remote work, require the right technology to make it easy for employees to work together. HBR found that collaborative work has risen over 50% in the last decade and now makes up 85% of the average worker’s time. Advanced communication and collaboration tools facilitate seamless teamwork and information sharing, streamlining processes and reducing the time and effort required to complete tasks. Teams working in different locations, including separate office locations and home offices, can now work together as well (or sometimes better) than if they’re under the same roof without the right technology.
- Data-driven decision-making: Manufacturing leaders must make many decisions each day, often very quickly. By using data analysis and visualization, you can make more informed decisions, optimize processes and eliminate inefficiencies, ultimately reducing costs. According to The Global State of Enterprise Analytics, the majority (56%) of organizations surveyed said that data analytics improve the speed and effectiveness of their decision-making.
- Predictive maintenance: When a machine stops working correctly, your factory experiences unexpected downtime. Additionally, if a machine is not working correctly, the quality of the production may be lowered, which costs time and reduces customer satisfaction. By using IoT devices and sensors, you can monitor equipment performance and predict potential failures. If you discover that a machine needs proactive maintenance, you can preventatively service the machine or use a backup, which reduces the costs associated with downtime and reactive repairs.
Understanding your TCO for each asset and proactively working to reduce this number provides many benefits to your manufacturing organization. By implementing the right technology, you can significantly lower your TCO, which can greatly reduce your overall expenses.
Successfully integrating new technologies into your manufacturing organization starts with the right infrastructure, and the right partner. With a partner to provide reliable connectivity, dependable communications, advanced security and the trusted expertise you need, you can focus on what you know best—most efficiently manufacturing the highest quality products.